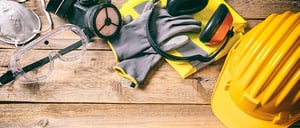
The Commercial Building Owner's Guide to Roof Replacement
TABLE OF CONTENTS
INTRODUCTION
As a building owner, your commercial roof is one of your most expensive investments. Your roof not only protects your building—it ensures that your operations and employees can continue to execute the important functions you need for your business to be profitable. It is all too easy to forget about what’s over your head when you are busy running a business under that roof.
We are providing commercial and industrial building owners with this e-book, The Building Owner’s Guide to Roof Replacement, to help you get the safest, longest and most productive life out of your roof.
The six chapters in this e-book are:
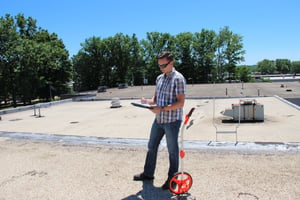
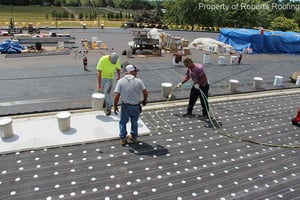
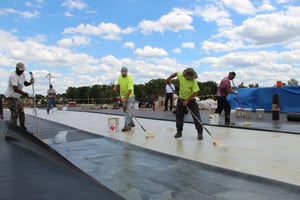
DO I NEED TO REPLACE MY COMMERCIAL ROOF?
While every building owner hopes that their new commercial roof will last for decades to come, external factors can sometimes cause damage over the lifetime of the flat roof. Problems also can surface when a commercial roof hasn’t been properly maintained or when the wrong system was selected for that particular roof.
Here are four questions we ask our customers in guiding them toward the best solution:
1. What is the extent of damage?
2. Where is the damage, and how does it affect the building’s use?
3. Is the owner looking for a short-term fix or a long-term solution?
4. How much will the work interrupt business processes?
When problems occur, the commercial building owner and facilities manager often must weigh the pros and cons of roof repair versus roof replacement. Other than cost, what are the most important issues to consider in making the right decision?
Extent of Damage
If the majority of your roof is still in sound shape with good insulation, it may be possible to get by with a repair. For example, on a built-up asphalt roof system, several torch-down patches may be sufficient enough to cure a serious leak without the hassle of replacement. Additionally, when you simply want to extend the life of your building’s roof, a cost-effective coating might make sense.
However, the general rule of thumb is that if 25% or more of the roof is damaged, it’s more cost-efficient to replace the entire roof. Further, if the damage is severe, the insulation is either wet or not performing—or if previous repairs have not held up, it is time for a full replacement.
Location of Damage
Is the damage located over an area of the building that is critical to your business operations? Or, are the problems located over an expensive piece of manufacturing equipment? If you have previously repaired this area before and continue to incur damages and business interruptions, you may need to consider a full replacement or, at the very least, a re-cover.
Business Interruption
If a leak occurs during the busiest time of year for your business—for example, January through April for an accounting firm—you may decide to delay replacement by making the most essential repairs now and scheduling a full replacement at a time when that work would cause the least amount of business disruption.
With many options to consider, you want to work with a qualified, experienced and innovative roofer that will walk you through each of these options. No two roofs are alike, so make sure you are not getting a one-solution-meets-all quote.
Once you make the decision to replace your roof, you will want to hire the best commercial roofing company to get the job done efficiently, safely and professionally.
Owner’s Occupancy Outlook
If you have plans to sell the property in the next two years and can reasonably repair the roof to meet code inspection, a routine maintenance procedure would be recommended. This would include the patching of minor leaks and proactively repairing anything that may be deemed a future liability. However, most owners aren’t eager to relocate after all the investments they have made in a building, not to mention the significant interruption to business a major move requires. If you are seeking a long-term solution with the latest technologies, it simply makes more sense to replace the roof.
HOW DO I HIRE THE RIGHT COMMERCIAL ROOFER?
Once you have made the decision to replace your commercial roof, determining which commercial roofer to hire is the next crucial decision. You will want to make sure you are hiring an experienced, reliable and professional company for long-lasting, cost-efficient results.
10 Considerations Before Replacing Your Commercial Roof
1. Expertise
- There are many successful residential roofing contractors who do excellent work. However, residential and commercial roofing are as different as night and day when it comes to materials and application techniques. Residential roofing companies do not have the ability to properly install a commercial industrial roofing system that will remain watertight for a minimum of 20 years. The materials and equipment in use today, when installed properly, will easily surpass that expectation if the roofing contractor installing them has the requisite experience, training, resources and manufacturer support.
2. Training
- Successful commercial roofers spend hours in continuous training. State and federal regulations require commercial roofing contractors to have training in hazard communications, fall safety, rigging and signaling. Trainers also cover proper job setup and operation of equipment ranging from telehandlers to lift platforms to large cranes and trucks. Your commercial roofing contractor should also have regular training as per material manufacturers to stay updated on the latest materials and techniques. This will help the roofer guarantee a long-lasting roof system and stay in compliance with the manufacturer’s installation requirements.
3. Communication
- Reliable commercial roofing companies will thoroughly communicate their approach to a job so that you can minimize disruption to your workforce and plan for any necessary rerouting. You should know whether or not your roofer is going to show up on a day with questionable weather. If the crew is running late, you should expect a call well ahead of arrival time. Good roofing contractors are in touch with their customers at all times. You have a right to expect your commercial roofer to be on time and on budget, with minimal disturbance.
4. Safety
Your commercial roofer should train their staff and stay updated on safety and injury prevention techniques—not just the safety of the workers, but the safety of your building and the employees inside of it. For example, Roberts Roofing conducts bi-monthly mandatory safety meetings from December through April to review job-specific safety issues and industry updates. We also hold weekly job-specific meetings on the worksite through the duration of your project. Before a job begins, your roofer should review safety plans with your facility personnel. For example, we incorporate your safety policies into our weekly meetings.
5. Innovation
- There is no one-size-fits-all approach to roofing jobs. Roofs vary in dimension, design, age, materials, problem areas and special considerations below the area over which we are working (i.e., clean rooms, vibration-sensitive manufacturing processes, or human concerns, such as the need for quiet in healthcare settings, offices and schools). Commercial roofing is field-fabricated on-site to fit your particular building. While the materials are the same, the difference is the experience level of the field technicians who are fabricating them to fit your roof. You want a commercial roofer with the experience level to consider your particular needs and then customize a solution for you so that you can avoid problems that will occur in later years, costing you unnecessary expense.
6. Maintenance
- The contractor you choose to work with is paramount to the life expectancy of your roof. Your contractor’s maintenance crews should hold current certifications in roofing repair techniques and training, and be knowledgeable in all types of roof systems, including PVC, BUR (built-up roofing), modified bitumen, metal, and EPDM. Further, you want to hire commercial roof maintenance technicians who are trained and experienced in investigating potential problems that will cause roof leaks in the future. They should know what to look for and how to repair the problem according to the roofing system manufacturer’s specifications.
7. Availability
-
Demand has outpaced supply on a variety of roofing and building materials in recent years. The 2018 government-imposed steel tariffs on imported steel narrowed the supply, which was compounded exponentially due to slowdowns in the global economy when the COVID-19 pandemic hit. Those slowdowns are expected to continue through the remainder of 2022 and possibly well into 2023. Though the Section 232 steel tariffs were mitigated in May of 2022 with passage of tariff-rate quotas (TRQ) allowing more steel imports, there is a lot of catching up to do.
In addition to steel, the global supply chain shortages continue to affect availability of a wide variety of roofing materials including copper, aluminum, wood, and asphalt. Placing orders as soon as a problem is discovered with your roof can help ensure you get needed materials as soon as they are available.
8. Commercial Roofing Equipment
Your roofer should have the right equipment for your specific needs. For example, Roberts Roofing has over $2 million in equipment to meet the needs of all the customers we serve. Roberts Roofing believes investing in and utilizing the right equipment for each scenario makes the job safer for our employees and the customers we work for. For example, we would use a crane to load a 500-lb. piece of equipment onto your roof instead of pulling it up the side of a building.
9. Compliance
- All industrial roofers should be in compliance with federal, state and local requirements and roofing guidelines, and hold every updated certification that a project may require, such as proper crane operation or safe asbestos removal from roofs. Most roofing companies have to comply with the drug-free workplace requirement which requires random drug testing that is documented according to state guidelines.
10. Qualifications
-
Your commercial roofer should be in good standing with the top commercial roofing manufacturers. The roofer should have written documentation stating that they are approved contractors to install the manufacturer’s roofing systems and provide the highest warranty available from that commercial roofing manufacturer. If approved, your commercial roofer will have that documentation with a current date. You should also ask for a list of completed jobs that are similar or greater in scope of work than your project. Ask some questions, require documentation and get to know the contractors bidding on your roof project. Better yet, do some background checking on references and—when possible—visit the contractor’s headquarters. Ask to see a job that is currently in progress. The time and effort you invest will be well worth a roof that will produce returns for more than 20 years.
While your commercial roofing contractor can help you choose the best roofing system and materials to meet your particular needs, it is advantageous to have a good working knowledge of the best commercial roofing system and material options to meet your specific needs.
WHICH COMMERCIAL ROOFING SYSTEM SHOULD I SELECT?
Commercial roofing became a specialized trade in the mid-19th century. Through the years, many roofing systems have come and gone. There are certain considerations to keep in mind as you work with your professional commercial roofing contractor to determine your roofing system and materials:
- How long do you plan to occupy the building?
- What is your intended use for the building?
- What characteristics define the surrounding environment? (e.g., airport proximity, harsh chemicals, temperature variations)
- Does the federal, state or local government provide tax incentives for alternative roof designs for greater energy-efficiency or green products?
The answers to these questions will dictate the quality of materials you use—a very important factor in determining the life expectancy of a roof. For example, you’ll want to choose materials that will work well with both the intense UV rays we experience in the summer, as well as harsh winter weather conditions.
The first thing you want to consider is the type of facility you own. Is it a major manufacturing facility with many rooftop exhaust fans and units that require constant foot traffic to maintain them? Is it a warehouse used for storing products, equipment or materials? Is it an office space where the comfort of individuals is a priority? Next, factor in your ownership intentions—do you plan to keep the facility indefinitely, or do you plan on selling in the near to immediate future? Finally, define your budgetary parameters. From there, you can evaluate roofing system types for potential inclusion in your overall project framework.
There are many options when it comes to selecting the right roofing system for your commercial or industrial facility. However, only two variants hold up the longest and provide the best value.
Single-ply Roofing Systems
Single-ply roofing systems are the current preference in the roofing world. They are affordably priced, durable and can be warranted in excess of 30 years. They are comprised of products like TPO, PVC and EPDM. These products are much cleaner to apply than raw asphalt-based products and in the case of TPO, are rated to hold up to the accumulation of standing water. While TPO and PVC are primarily available in white to reflect sunlight and keep your roof cool, other assorted colors are available to suit your facility. These products are best suited for offices and warehouses where roof traffic is limited, but they also are compatible with essentially any commercial structure.
Asphalt-based Roofing Systems
Asphalt-based roofing systems have been around for over a century, and were previously the industrial roofing standard. They are thick, messy (a good thing, since that means multiple layers of heated or cold-based asphalt) and, most important, resilient. When properly maintained, it’s not uncommon for a built-up asphalt roof to last over 50 years.
Asphalt-based roofs are composed of layers of modified or fiberglass rolls, which are set and covered in hot or cold asphalt and then capped with gravel or an additional asphalt-based granulated cap sheet. They are commonly found on educational institutions and manufacturing facilities. The pricing for asphalt-based roofing systems can be volatile at times because they are linked to the current world values of petroleum—the primary ingredient in their required materials. That being said, they are sometimes slightly more expensive than their single-ply counterparts, but not by much, depending on the exact specification applied.
UNDERSTANDING COMMERCIAL ROOF WARRANTIES
As we have discussed, there are numerous commercial roofing systems available and, as a result, there are hundreds of applicable roofing materials. The type of materials used on your commercial roofing system determine your warranty.
Most reputable commercial roofing materials manufacturers offer 10, 20 and 30+ year warranties for their roofing systems. These warranties are determined primarily by the thickness, durability and overall quantity of materials used.
A 20- to 30-year warranted commercial roofing specification generally requires an abundance of materials applied to the roof surface. This ensures the finished product will go the distance and, with proper annual maintenance, extend beyond the number of warranted years issued. A 20-year warranted asphalt roof system has been known to last well over 40 years when properly installed and routinely maintained.
For example, a GAF Corporation recover of an existing asphalt roof with dry insulation would require a four-ply fiberglass felt, with each layer set individually in 25 pounds of hot asphalt per ply per 100 square feet. As installed by the certified professionals at Roberts Roofing Company, this “board-over” of the asphalt roof is warranted by GAF for 20 years.
For single-ply membranes, membrane thickness is the key to a long roof life and 20+ year warranty. For example, a GAF Corporation .060 mil, white TPO membrane paired with the GAF RhinoBond fastening system, installed by the certified professionals at Roberts Roofing Company, will garner a 20-year warranty. And with routine and proper maintenance, the materials will last long beyond the warranted mark. TPO thickness varies from the thinner .045 mil, all the way to the .080 mil, and beyond. The thicker the membrane, the tougher the membrane, and the longer the warranty.
Thicker specs and membranes generally require greater know-how from your commercial roofer. It is always smart to check with your commercial roofing materials manufacturer to see if your commercial roofer is certified, let alone capable to apply such detailed roof specifications.
Roberts Roofing has been certified MasterSelect by the GAF Corporation and holds many other certifications for the toughest and thickest roof systems available from all of the major commercial roofing material manufacturers.
Now that you have a basic understanding of how commercial roofing warranties work, let’s take a look at why ongoing roof maintenance is essential.
INSPECTING AND MAINTAINING YOUR FLAT ROOF
Just like an automobile, a new roof is a large capital expense. Think about it—you wouldn’t spend $50,000 or more on an automobile and never get it serviced. As a building owner, your commercial roof is one of your most expensive investments. Just as you schedule regular maintenance checks for your car or home, regular maintenance of a flat roof will help to prevent costly and premature repairs. After all, your roof not only protects your building, it ensures that your operations and employees can continue to execute the important functions you need for your business to be profitable.
To get the most value out of your commercial roof investment, you need to maintain it.
Manufacturer warranties require periodic maintenance with repairs, at the owner’s expense, to maintain the warranty. Maintenance and periodic roof inspections will also increase the life expectancy of the roof system beyond the warranty period.
First Line of Defense
Think about the protection your roof is providing your business operations. If something goes wrong with the roof, chances are that at least one business process is interrupted. You want to count on your roof protecting your building from harsh weather elements and other unexpected hazards.
Make Needed Repairs
Regular inspections and maintenance of your new roof will, in many cases, isolate specific problems that only need a repair. Why take the chance of letting something develop into a bigger problem that necessitates the need for a total roof replacement?
Inspection Frequency
All commercial roofs, including new roofs, should be inspected every six months to ensure early detection of a problem. There are many external factors beyond your control that can contribute to damage—think in terms of severe weather, heavy foot traffic and accumulated debris from the surrounding area. Your contractor should look for signs of potential leaks, defects, and threats from surrounding trees or other equipment, as well as anything else that inhibits adequate drainage.
Know Your Warranty
Get your manufacturer warranty in writing and be sure you understand what the warranty covers when your new roof is installed. Just as you would with an automobile, keep a careful record of all your inspections and any repairs made—you’ll be glad you did in the long run. We’ll provide more information about commercial roof warranties in the next chapter.
Careful maintenance of your new commercial roof will identify issues before they become major problems. While you may some incur some short-term costs to maintain your roof, investing in ongoing maintenance now will provide significant cost savings and add years to the life of your new roof. By conducting maintenance at regular intervals, you can have confidence that you are protecting all of your valuable assets inside the building.
Roberts Roofing Company strongly recommends yearly maintenance for your new commercial roof system as well as preventive maintenance for your existing commercial roof system. Once in the fall and once in the spring is a good rule of thumb, and remember—annual maintenance with inspection will prolong the life of your new roof.
Roberts Roofing is committed to helping commercial building owners and facility managers keep their roofs in top operating condition. From regular inspections to repair and replacement, we can provide guidance about the steps you can take to prolong the life of your flat roof.
Learn About Our No-Obligation Roof Inspection
FACTORS AFFECTING THE LIFE CYCLE OF A COMMERCIAL ROOF
When commercial building owners consider the investment in their commercial roof, they often consider the initial cost of installing or replacing the roof and the warranty that is included with installation. The quality of workmanship and the material you use will go a long way in extending the life of your roof.
However, there are many other factors to consider when looking at the overall life cycle of a commercial roof, such as our Northeast Ohio weather, inspections and repair costs.
If a flat roof is expected to last roughly 20 years but begins to incur substantial maintenance cost in the latter five years—or even needs a total roof replacement—then the life cycle cost increases.
The roofing professionals at Roberts Roofing Company recommend five tips for prolonging the life of your flat commercial roof.
Invest in Regular Roof Inspections
Weathering, deterioration and heavy foot traffic are just a few factors that can contribute to problem areas. In addition to the regular checks your facilities manager (if you have one) makes, be sure that a professional roofing contractor inspects your roof twice per year. By carefully examining all roof areas, from the perimeter to the center, the contractor will be able to spot signs of problems such as damaged flashing.
Protect the Roof Surface
Be sure to limit access to the roof. Obviously, there will be other contractors that need access to the roof surface, such as HVAC workers, satellite dish installers and electricians. Designated walkways, padding and railings can help keep other contractors away from more sensitive areas. That being said, we advise inspecting the roof surface following such visits to determine whether any damage was inadvertently caused by heavy foot traffic or the penetration of the roof surface.
Maintenance Checks
When you have a warranty with a commercial roofing contractor, be sure you understand everything that is covered and for how long. Keep in mind that you have obligations under the contract. The last thing you want to do is void your contract by not conducting inspections or reporting damage.
Don’t Delay Repairs
That small pool of water near a drain may not seem to present much of a problem today. Don’t wait until the weight of excessive water leads to a potential roof collapse. Have someone inspect the roof after extreme weather conditions of a rough winter with freeze-thaw cycles. You might have to fork over the money to make repairs, but that’s far better than paying for a roof replacement later.
Promote Water Flow
As part of your roof inspection, make sure that all water runoff is working efficiently. Check that all gutters, drains and downspouts are kept clear and clean at all times.
CONCLUSION
The roof on your commercial building is your first line of defense from many natural and man-made disasters. It is also the most exposed part of your building as it is subject to elements that can contribute to its deterioration. Be sure to have your flat roof inspected on a regular basis for repairs that need to be made. When it comes time to replace your roof, we hope the information in this e-book provides you with a valuable guide to understanding what’s involved with commercial roof replacement.
Roberts Roofing Company has been a leading provider of innovative commercial and industrial roofing solutions in Cleveland, Ohio since 1981. We serve companies of all sizes In Cleveland, Ohio and the surrounding region with full-service commercial roofing services, offering a combination of technical expertise, custom solutions and quality workmanship to every project. Our team consists of nearly 40 fully trained roofing professionals. While we take great pride in our years of experience, we strive to stay up to date on the latest roofing practices and safety standards.
For more information about commercial roof replacement, repair or maintenance, give us a call at 440-946-2233, email info@robertsroofing.com, or contact us using the form below.